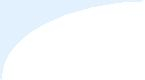
Сварка
Не совсем лирическое отступление
В детстве мечтал быть космонавтом, сварщиком - не мечтал. Один сосед, профессиональный сварщик с многолетним опытом работы, думая, что я один из них, интересовался, где находится моя сварочная мастерская в городе... Я в ответ пожаловался, что в серверной нет розеток на ток 50 ампер, да там и паять-то нечего, не то что варить. Все модульное - вентилятор на блоке питания Sun сервера стал медленно вращаться, заменим блок питания. Для сравнения стоимость вентилятора примерно $20, а стоимость блока питания - $420. Вот это бизнес! Вот это по-нашему, по-канадски!
Я так думаю, что если бы картриджи для струйных принтеров не стоили бы половины стоимости принтера, то принтеры бы давно стали выпускать одноразовые. Хотя здесь я, конечно, не прав. Как любой расходный материал, себестоимость картриджа раз в пять-десять меньше его рыночной стоимости. Принтер же продается по себестоимости только для того, чтобы потом сделать деньги на картриджах. Точно также сотовые телефоны раздаются бесплатно, а деньги делаются на продаже услуг сотовой связи.
Вентилятор же почему-то не считается расходным материалом, хотя это один из наиболее часто ломающихся компонентов блока питания. И вот он деловой подход: вместо того, чтобы сделать вентилятор легко заменимым дешевым элементом дорогостоящего блока питания, предлагается менять сам блок питания. Гениально! Остап Бендер просто отдыхает...
Полякевича тут, конечно, понесло...
О сварке и сварочнике
Ну так вот, о сварке. Я никогда в жизне не варил. И никогда этим не интересовался. Пришлось опять понабрать книг в библиотеке и видеокассет. Как выяснилось, что наиболее легко осваиваемым способом сварки, дающим приемлемые результаты является электрогазосварка, по английски MIG или GMAW. Газ в основном служит защитным элементом, это или CO2 или смесь СO2 c азотом. Сама сварка электрическая: невысокое постоянное напряжение 15-25 вольт и высокий 100 - 300 ампер ток. Чем толще материал, тем выше нужен ток.
В моем случае самые толстые листы стали - 6 мм. Для них нужен ток порядка 200 ампер и напряжение 20 - 25 вольт. При выборе сварочника важно еще, чтобы он не только обеспечивал необходимую мощность, но еще и не перегревался слишком быстро, иначе придется 2 минуты варить, потом 8 минут ждать пока он остынет.
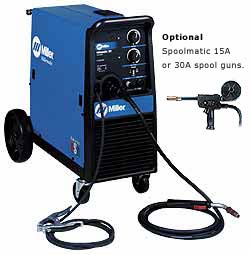
Всем известно, что в Северной Америке напряжение питание 110 вольт, но мало кто знает, что это только в обычной розетке. В дом приходит два таких напряжения, которые если сложить, то получится 220 вольт, как и в большинстве стран мира. Электроплита или сушилка в большинстве северо-американских домов тоже работают от 220 вольт. Поэтому теоретичеки всю российскую технику, рассчитанную только на 220 вольт, в Америке можно подключить без особых проблем. Это я все узнал пока дом строил. Поэтому сделать проводку на 220 вольт для сварочника не составило большого труда. Одну розетку я сделал в гараже, а другую на улицу вывел.
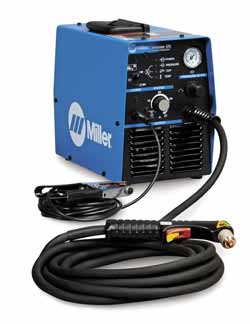
Остановился на двух моделях, наиболее популярных в Америке: Miller Millermatic 251 и Lincoln Electric Power MIG 255C. На Miller были скидки, поэтому купил его, а также еще и аппарат для плазменной резки метала того же производителя.
Проба пера
Из прочитанных книг, я сделал вывод, что наиболее важно для качественной сварки - это сохранение постоянного расстояния между пистолетом и материалом, а также скорости перемещения пистолета вдоль шва. Мне казалось, что эту проблему можно легко решить, изготовив тележку для пистолета, что собственно и используется в промышленности для автоматизации сварочных работ. Однако опыт показал, что твердая рука сварщика лучшей всякой тележки!
Безгазовая сварка
Безгазовая сварка - это то, что нужно для постойки яхты под открытым небом килем вверх. По своему принципу она очень похожа на традициооный способ сварки углеродистыми стержнями (stick welding), но по качеству не уступает газоэлектросварке типа MIG. При безгазовой сварке используется специальная проволока с начинкой (gasless flux-cored wire), которая защищает место сварки от пагубного воздействия атмосферы вместо буферного газа. Существует два (на самом деле больше) типа проволоки с начинкой (flux-cored): первый требует использования газа (flux-cored wire), второй (gasless flux-cored wire) - нет. Второй тип наиболее дорогой.
Основные преимущества безгазовой сварки:
- Можно варить в любой ветер. Для такой сварки ветер - даже хорошо, так как он сдувает вредные пары, что важно. В отсутствии ветра или при сварке в закрытых помещениях обязательна хорошая вентиляция, что в принципе важно при любом типе сварки.
- Как и при сварке обычным электродом, легкая ржавчина - не помеха.
- Варить потолочные швы также легко как и не потолочные, честное слово, никакой разницы!
- Варить можно без наконечника для газа, что очень удобно, так как он не мешает варить в узких местах.
- Не нужен тяжелый газовый баллон. Перемещение сварочника занчительно облегчается, особенно внутри корпуса яхты.
- Безгазовая сварка требует значительно меньше электроэнергии, т. е. рабочие напряжние и ток гораздо меньше, чем при газовой сварке. Поэтому в зависимости от модели сварочника можно варить практически непрерывно, не боязь перегреть сварочный аппарат. Несмотря на низкий ток, глубина безгазовой сварки больше, чем газовой.
Из недостатков я бы назвал следующие:
- Много вредного дыма, нужна хорошая вентиляция.
- Безгазовая сварка медленне, чем газовая, соответсвенно нагрев металла немного больше. Обязательно следовать основным принципам сварки, чтобы избежать деформации металла из-за нагрева.
- Безгазовая проволока дороже, чем обычная.
На североамериканском рынке я видел два типа безгазовой проволоки: E71T-GS и E71T-11. Первый тип применяется в основном для сварки тонкого гальванизированного металла, второй более универсальный. Из моего опыта могу сказать, что E71T-GS не годится для сварки яхты, потому что когда швы остывают, они просто трескаются, что не только хорошо видно, но и слышно! E71T-11 - это то, что нужно.
Стачивать или зачищать?
Вопрос, можно сказать риторический. В прошлом считалось, что внешние сварные швы, которые ниже ватерлинии, стачивать не надо, чтобы не уменьшать прочность и водостойкость шва. Сегодня большинство придерживается противоположной точки зрения. Ну, а как на счет внутренних швов?
Сквозные швы, которые ниже ватерлинии, обычно проваривают с обеих сторон и их, на мой взгляд, нужно только зачистить изнутри, так как они уже сточены снаружи. Вопрос больше по поводу сварки между обшивкой и набором. Нужно ли стачивать их до гладкой поверхности или нет?
Тут возникают два момента. Гладкая повехность, по идеи, должна обеспечить хорошее основание для грунтовки. С другой стороны, стачивание швов до гладкой поверхности невольно их утоньшает и, тем самым, делает слабее.
Помимо двух слоев грунтовки, изнутри корпус покрывается теплоизоляционной пеной и таким образом, места сварки теоретически должны быть защищены от механических воздействий и влаги. Вопрос тогда стоит такой: как современные грунтовки ведут себя в таких условиях? Не смягчает ли такая защищенная среда требований к поверхности?
Производители краски обычно оговаривают степень очистки поверхности для различных условий эксплуатации: чем жестче условия, тем тщательнее должна быть подготовлена поверхность. Я думаю, что этот принцип можно распространить и на степень гладкости.
Если считалось, что внешние подводные швы можно было не стачивать до гладкой поверхности, то уж внутренние швы, которые находятся в гораздо более выгодных условиях наверняка можно не стачивать, тем более, что в углах "болгаркой" так или иначе не возьмешь.
Внизу три фото. На первом показан шов сразу после сварки безгазовым методом. На втором - тот же шов, но уже зачищенный с помощью проволочного диска-щетки. Пескоструй, вероятно, способен на большее. На третьем - тот же шов, сточенный болгаркой.
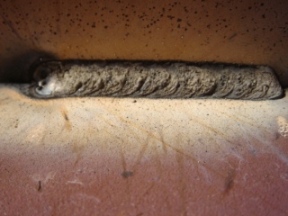
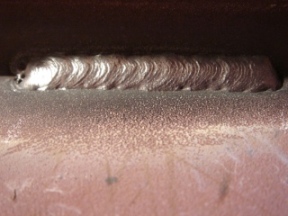
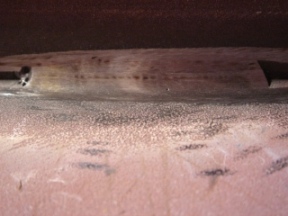
Последний шов, конечно, выглядит привлекательно на мой взгяд по сравнению со вторым. А как на взгляд грунтовки?
- Какая грунтовка одинакого хорошо ляжет и на ту и на другую повехность?
- Или какое семейство цинковых грунтовок (органические, неорганические, эпоксидные) наиболее подойдет, учитывая что поверх будет напыляться теплоизоляционная пена?
- Стоит ли использовать проникающие грунтовки на эпоксидной основе или на освнове сульфата кальция?
Финальная сварка
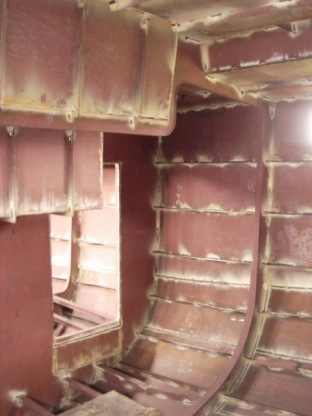
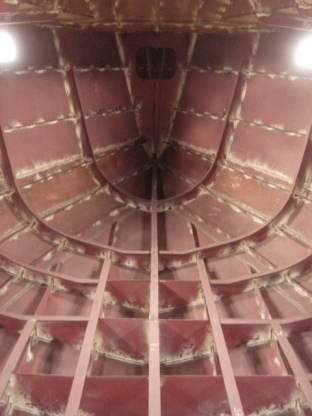
Финальная сварка заняла почти все лето, в свободное от основной работы время, конечно, то есть вечерами, по выходным и во время двухнедельного отпуска. Шпангоутная конструкция - вещь трудоемкая, вне всякого сомнения. Но 350 частей для корпуса длинной 38 футов - это все же многовато. К тому же, в это набор не входят детали иллюминаторов, окон рубки, люков, дверей, фальшборта, бушприта и т. д. Я сравниваю все это с бесшпангоутными конструкциями типа origami boats. С другой стороны, корпус получился очень прочным и жестким, что мне безусловно нравится и что было одним из требований ТЗ.
Узлы соединений
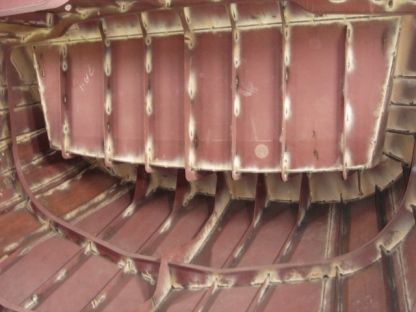
Как видите, фланцы приварены повсюду, по крайней мере, по всему периметру шпангоутов. Узлы, где детали продольного и поперечного наборов пересекаются, проварены со всех сторон. Брюс настаивал, что от них зависит прочность всей конструкции. Бимсы флора - т-образные, 50x50x5 мм на расстоянии 30 см друг от друга.
Усиление листов
Большинство листов усилено с помощью перпендикулярных полосок 25 - 40 на 4 мм. Стрингеры - 50 на 5 мм. Фальшкиль - 100 на 5 мм - приваренный с обеих сторон к обшивке сплошным швом.
Швы ниже ватерлинии
Ниже ватерлинии все швы проварены сплошным швом с обеих сторон. Было даже искушение проварить и остальные швы так же. Филе-швы выше ватерлинии проварены только с одной стороны, а угловые швы - прихвачены еще и с обратной стороны 5-см стежками каждые 10 см в соответствие с инструкциями разработчика.