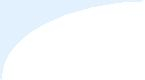
Руль
Сбаланированный или не сбалансированный
Писал письмо Брюсу, спрашивал, можно ли несбалансированный руль Вояжера на скеге переделать в сбалансированный. Брюс ответил без комментариев, что сбалансированный руль - это плохая идея. Я, честно признаться, слегка удивился, так как во всех книжках написано как раз наоборот. Сбалансированным рулем легче управлять, меньше нагрузка на элементы управления, меньше расход энергии у автопилота. Единственным достоинством несбалансированного руля, с моей точки зрения, является его свойство всегда стремиться занять положение параллельное корпусу яхты. Таким образом, если рулевой, например, выпал за борт, то яхта в большинстве случаев приведется к ветру и остановится.
Если у кого другие мнения по поводу двух типов рулей, напишите, пожалуйста.
Спасибо Earendil за популяное обяснение гидродинамических особенностей обоих типов рулей. За счет скега поток воды обтекает несбалансированный руль более ламинарно и поэтому создается большая подъемная сила или вращающий момент. Таким образом, размер несбалансированного пера руля может быть меньше, чем сбалансированного, и соответсвенно сопротивление он будет оказывать меньшее.
Теперь ответ Брюса принимает здравый смысл. Если я решу использовать Hydrovane в качестве самоуправляющей системы (windvane), которая имеет дополнительный сбалансированный руль, устанавливаемый с кормы, то автопилот можно будет присоеденить к нему.
"Самоотваливающийся" скег
Брюс, по крайней мере в прошлом, разрабатывал свои проекты, используя идею "самоотваливающегося" в случае аварии скега. Как показал опыт, такой скег редко отваливался без сопутствующих повреждений корпуса и иногда даже отваливался в условиях, которые трудно классифицировать как аварийные.
Несмотря на то, что купил я набор Брюса всего пару лет назад, Вояжер 388, будучи относительно новым проектом, все-таки унаследовал эту идею. Скег приваривается к дну между 9 и 10 шпангоутами, где отсутствуют какие-либо усилительные элементы. Изменяющаяся нагрузка на скег приводит к усталости металла из-за постоянных небольших изгибов в противоположных направлениях. Таким образом, дно корпуса просто ломается раньше, чем сварные швы. К тому же, это известный факт, что сварные швы могут быть крепче свариваемых частей.
Сама идея "самоотваливающегося" скега кажется не вполне понятной. Даже если скег отвалится без повреждений корпуса, потеря управления может быть фатальной как для яхты, так и для ее экипажа.
Недавно Брюс разработал новый тип "безопасного" скега, где нижняя часть скега крепится к килю при помощи мощной стальной балки. Он, видимо, прочитав мои комментарии на этом сайте, предложил бесплатно модификацию для моего Вояжера. Что-то мне не нравилось в идее балки между килем и скегом. Во-первых, она достаточно длинная, т. е. держать скег будет плохо. Во-вторых, дополнительная подводная деталь, подверженная столкновению с плавающими мусором и подверженная риску поломки при посадке на мель. Того и гляди, сама погнется, да еще и киль или скег повредит.
Вместо этого я думаю усилить дно между 9 и 10 шпангоутами. Точнее, сначала приварить вокруг места крепления скега к дну уголок из стальной полоски, чтобы увеличить площадь крепления, потом по периметру этого уголка изнутри приварю удлиннение скега, симулируя сквозной скег. Это удлиннение внутрь корпуса разопру уголками поперек днища, чтобы предотвратит проблему усталости металла.
Детали пера руля
Ось руля желательно делать из нержавейки типа 329 диаметром 2,5 дюйма. См. Выбор материала для руля. Возможные варианты конструкции можно посмотреть на веб сайте Тайдс Марин. Подшипники типа G or H могут быть использованы на скеге.
После переписки со службой поддержки Тайдс Марин, я решил что потребуется три подшипника: тип E - вверху, тип G - посредине позле дна и специальный подшипник, не показанный на их веб сайте для скега.
Несмотря на то, что нержавейка 329 прочнее, чем 316, я приобрел 316L. 329 у нас не продают. Прочность будет обеспечена конструкцией скега.
Сначала - каркас, а потом - обшивка!
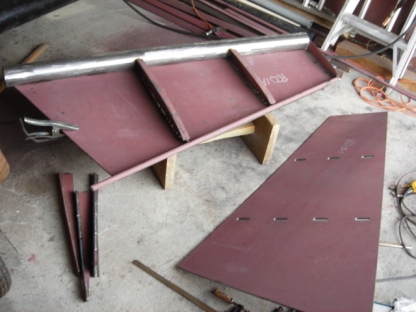
Уже сентябрь, а я только взялся за руль, который порывался сварить еще прошлой зимой в гараже. Казалось, что все продумал в смысле крепления пера руля к скегу и скега к корпусу. Не учел только "главного" принципа металлоконструкций. Читайте дальше, что в результате получилось. Надеюсь, что мой горький опыт пойдет кому-то на пользу.
У скега всего три ребра: одно внизу и два промежуточных посередине. Сначала я приварил полоски 25х4 мм к промежуточным ребрам. К ним будет привариваться обшивка правого борта через отверствия в обшивке. См. фото справа. Потом я приварил все ребра к левой обшивке, стараясь придать ей нужную форму. Потом к ребрам приварил 20-мм стержень с носа и 3-х дюймовую трубу с кормы. Трубу потом я планировал разрезать повдоль пополам. Цельная труба должна была меньше деформироваться при сварке. После этого перевернул конструкцию и приварил правую обшивку, стягивая передние кромки зажимами.
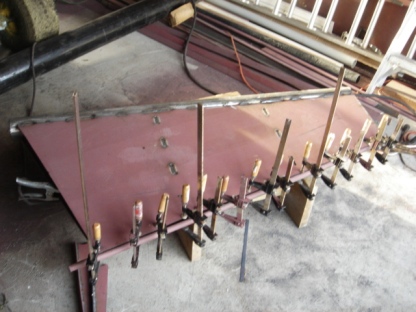
Сшитые сухожилия правой кисти прошли отличную проверку зажимами. Сухожилия выдержали, а вот кожа - нет. Многие зажимы тоже не выдержали. Пришлось помогать зажимными пассатижами и кувалдой. Газовая сварка внесла свою лепту нагревом металла.
Да, я снова переключился на газовую сварку дабы вспомнть, что это такое, ведь нержавейку придеться варить именно ей. Первое, что бросилось в глаза, а точнее, обожгло руки, это количество теплоты, выделяемое при газовой сварке. Второе - брызги металла, намного крупнее. Третье - меньше дыма, но больше яда в невидимом дыме, что не замедлило обернуться головной болью. Придется тоже варить в маске.
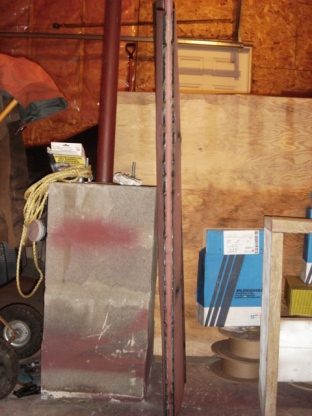
Стянув кромки, я поспешил проварить все швы до конца, так как уже было поздно и хотелось покончить со скегом именно сегодня. Когда же я поставил его вертикально, чтобы полюбоваться на законченную работу, то слегка обалдел - скег получился скрученным вдоль вертикальной оси! Это, конечно, невозможно было заметить в горизонтальном положении и тем более предотвратить, так как способ, который я выбрал для сборки скега фундаментально неверный.
Я читал в свое время как один товарищ делал перо руля. Он сначала приваривал ребра к новосой и кормовой трубкам, а потом уже наваривал на эту конструкцию обшивку. Конечно же, сначала - каркас, а потом все остальное! В моем случае листы обшивки, видимо, были скручены, и поэтому ребра оказались приваренными к трубе под разными углами.
Сначала я решил, что будет легче сварить новый скег, но потом обнаружил, что у меня не хватит не него 5-мм стали. Придется разбирать испорченный.
А надо было вот как
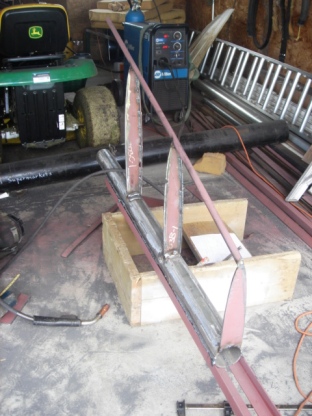
Ломать - не строить или "проверка сварных швов"
Как еще сварщик может проверить качество своей работы, не прибегая с современным технологиям неразрушающего контроля за сваркой?
Разобрать скег оказалось делом не хитрым. 6 5-дюймовых дисков для резки металла улетучились в один момент. Пришлось использовать более тостые шливовальные диски и плазморез. Через 5 часов скег был обращен в исходное состояние - швы оказались вполне достойными! Пришлось вырезать заново одно новое нижнее ребро и стержень для передней кромки. Трубу для задней кромки можно было использовать заново, повернув ее на 180°. Еще я вырезал вертикальные полоски для использования в качестве, если хотите, шпангоутов скега. В чертежах Брюса их не было.
Вторая попытка началась с фиксирования трубы двумя уголками и приваривания горизонтальных переборок строго по центру и строго вертикально. Потом приварил стержень носовой кромки сверху. См. фото слева.
Каркас получился что надо!
Ровно - не значит строго вертикально
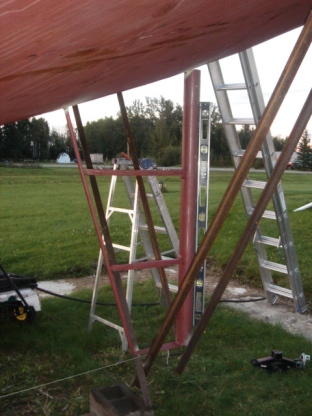
Следующим шагом должно было быть приваривание обшивки. Но я решил изменить последовательность сборки и приварить каркас к корпусу.
Решение, на мой взгляд, правильное. Тяжелый скег было бы куда труднее приваривать к корпусу. Около часа, наверное, ушло на выравнивание каркаса во всех плоскостях. Бетонные опоры слегка просели со временем и корпус уже нельзя было считать покоящимся в горизонтально-вертикальных плоскостях. Поэтому уровня было недостаточно, к тому же, он не такой уж и точный инструмент. Пришлось мерить расстояния от дна скега до фиксированных точек на скуле с двух сторон и добиваться их равенства.
Потом выравненный скег закрепил с помощью двух уголков с каждой стороны, чтобы не ушел в сторону при сварке. Уголки оказались также полезны для притягивания боковинок.
Обшивка скега
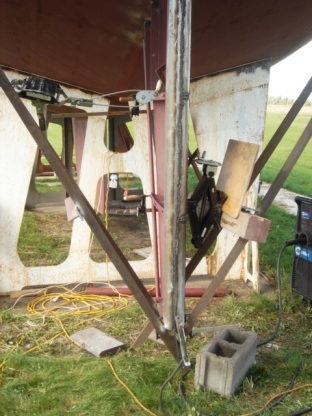
Можно было бы предположить, что первоначальная сборка скега должны была бы пойти ему на пользу при повторной сборке, так как листы железа были бы уже изогнуты по форме. Ничего подобного. Листы норовили свернуться в трубочку, только в направлении, перпендикулярном требуемому. Ради интереса я заглянул в файлы резки набора. Так и есть. Скег был расположен повдоль листа. Если предположить, что листы были горячей раскатки, то наблюдаемый феномен лекго объяснить. После нагрева сваркой металл стремился вернуться в исходное состояние, т. е. свернуться в рулон.
Раз уж разговор зашел о форме, то стоит заметить, что трех ребер явно недостаточно, чтобы придать 5-мм стали форму скега. Нужно, по крайней мере, пять, а еще лучше, использовать вертикальные ребра по типу шпангоутов. Тогда скег получится более гладким, без заметных перегибов.
"Шпангоуты" скега
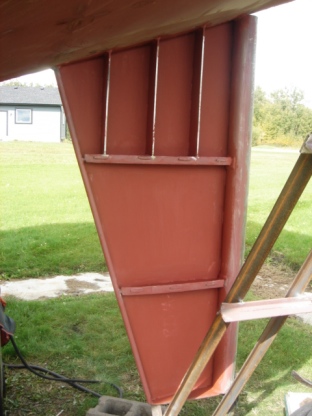
Я думаю многие слышали про сломанные рули. Не хотелось бы пополнить список потерпевших. Среди прочих способов усилить мой скег (см. ниже) я решил приварить его к корпусу подобно килю, т. е. использовать что-то типа шпангоутов. С внутренней стороны каждому из них, конечно же, будет соответствовать полоска металла от центральной линии почти до радиуса. Это необходимо для распредедения нагрузки на скег по как можно большему числу деталей набора.
Для шпангоутов скега я использовал 6-мм сталь, поэтому решил, что можно будет обойтись без фланца со стороны, где будет применяться метод сквозной сварки. С тому же, как мне кажется, в этом месте сварка не обязана быть очень прочной.
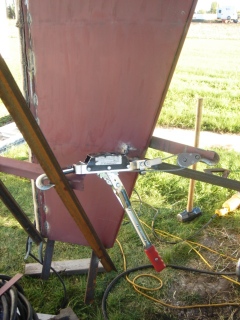
Формовка передней кромки скега на месте оказалась намного легче, чем с помощью зажимов. Обошлось без мозолей и сломанных стяжек на этот раз. Они просто не понадобились. Поступил также как и с килем - приварил кусок т-образной балки и использовал его в качестве рычага. Минимум усилий на лебедку. См. фото слева.
Уголок
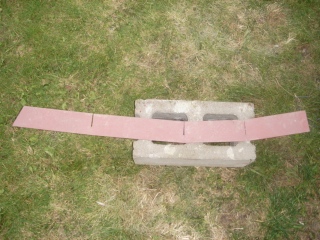
Другим элементом усиления скега, которым со мной поделился Браен Юнг на форуме общества строителей металлических яхт, был уголок, изготовленный из полоски 80х5 мм. Многие используют в качестве уголка четвертинку трубы, хотя полоска все же прочнее. Выглядит, конечно, не так красиво как четвертинка.
Со второй попытки удалось вырезать полоску, а точнее надрезать в нужных местах. Здесь сработал опыт, полученный при изготовлении фальшборта. Уголок увеличил площадь крепления скега к корпусу примерно на 4 дюйма. Общая максимальнаая ширина крепления теперь составила 8 дюймов, т. е. увеличилась вдвое.
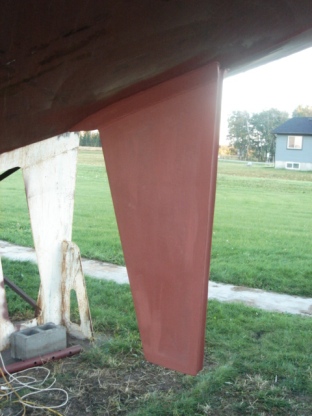
Ну, вот, скег почти готов. Труба отрезана, края зачищены, рыбка не порежется. Осталось решить вопрос с креплением нижнего подшипника. Есть мысль приварить его, а не париться с болтовыми соединениями, которые потом все равно приходится срезать болгаркой. Изнутри скег будет усилен во время установки рулевого колодца, а пока сварочник в гараже надо сварить сам руль.
Руль
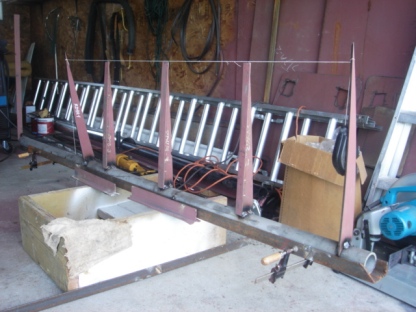
Печальный опыт изготовления скега должен был бы пригодиться при сварке руля, но не тут-то было. Работа с нержавейкой, сделанной в Китае, готовила новые неожиданности. Сварка ее с обычной сталью оказалось делом нехитрым. Я использовал проволоку марки 309L и чистый аргон. Получалось довольно неплохо.
Начал процесс, как и со скегом. Закрепил толстенную (sch. 80) 2-дюймовую трубу марки 316L, которая будет служить осью пера руля, горизонтально и приварил перпендикулярно ей ребра строго по линии.
После того, как я прихватил первый лист, я заметил, что ось руля деформировалась, по видиму, из-за сварки ребер с одной стороны. Пришлось выправлять.
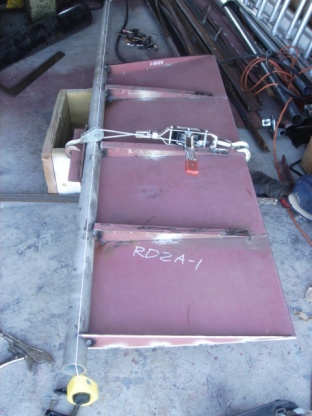
Сточил места сварки между всеми ребрами и боковинкой за исключением нижнего и верхнего ребер. Потом потянул двумя лебедками, как видно на фото слева, за ось. Достаточно было небольшого усилия, чтобы вернуть ось в исходное положение. Снова приварил ребра к боковинке. Что я не ожидал и обнаружил только после финальной сварки, так это то, что данный метод спрямления трубы вызвал ее кручение! Руль, как и скег в первом варианте, оказался скрученным вдоль своей оси! Не так сильно как скег, конечно, но все же заметно при внимательном рассмотрении.
Я бы не сказал, что наступил на те же грабли второй раз, скорее это были вилы. Помню, что когда проверял трубу с помощью нитки, то с удивлением обнаружил, что текст маркировки на трубе не следовал нитке. Я тогда списал это на несовершенство китайского разметочного оборудования.
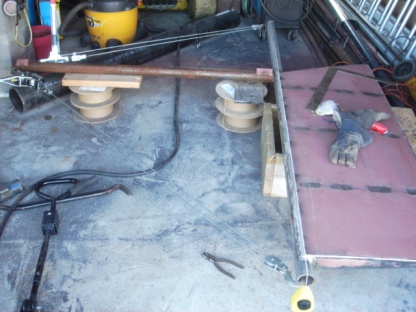
Заметно было то, что любая сварка с одной стороны трубы немедленно вызывала деформацию ее свободного конца. Справа более правильный способ исправления трубы, который не вызывает скручивание. Таким образом, фиксирование концов желательно для предотвращения деформации.
Теперь раздумываю о том стоит переделывать руль или нет. Больше беспокоит не то, что он скручен, а то, с какой легкостью он был скручен! Скег предохранит ось руля от поперечных деформаций, но не от скручивания. Как мне кажется, нагрузки на руль будут много больше, чем та, что я использовал для выпрямления трубы.
- Неужели нержавейка марки 316L - неподходящий материал?
- Или больший, чем рекомендованный разработчиком, диаметр нужно было использовать?
- Может нужно быдо использовать сплошной стержень, а не трубу?
- А может Китай производит некачественную сталь для Канады?
Если кто-то может что-то прояснить по этому поводу, напишите, пожалуйста.
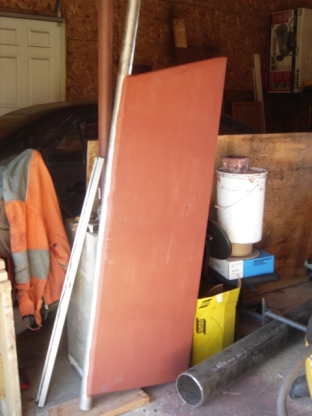
Вот он блестящий руль, поставленный в сторонку до выяснения обстоятельств. А пока займусь рулевым колодцем и усилением скега изнутри.
Я решил таки самостоятельно изучить вопрос деформации руля. Википедия, в английском вариате, дала ссылку на лекции университета Висконсин-Стаут по теории прочности материалов. Там нашел соответствующие формулы. Все, что от меня требовалось - это перевести их из имперской системы в Си. Вот ссылки на конкретные разделы лекций:
Да, сначала я оценил угол, на который мой руль свернулся. Скрутка совершенно не видна, если смотреть на руль спереди, т. е. она полностью находится в тени оси. Диаметр трубы, используемый для оси руля, 6 см плюс обшивка пол сантиметра с каждой стороны. Ширина руля около 60 см. Используя известные тригонометрические функции находим максимальный угол скрутки. Где-то 6 - 7° или π/30 радиан.
Вращающий момент вычисляется по формуле
T = φ x G x J / (L x g)
где φ угол вращения в радианах. G - модуль сдвига равный 77ГПа для стали марки 316L. Значение взято с данных по свойствам материалов. J - полярный момент инерции, который для трубы определяется по формуле
J = (π/ 32) x (do4 - di4),
где do и di внешний и внутренний диаметры трубы соответственно. L - длина трубы. В моем случае это расстояние между самым верхним и самым нижним ребрами, потому что труба скрутилась из-за того, что была закреплена между этими ребрами. g = 9.8 м/с2.
J = (3.14/32) x (1322 - 513) x 10-8 = 79 x 10-8 м4.
L = 1.5 м.
Получаем
T = (3.14 x 77 x 109 x 79) / (30 x 1.5 x 9.8 x 108) = 433 кг · м.
Так как я использовал 2-тонную лебедку, то вполне реально, что я создал такой момент, прилагая небольшое усилие.
Чтобы формула была действительна для рассчета вращающего момента на руль в реальной жизни, длина L должна соответвовать расстоянию от румпеля до верхней части руля. В моем случае это где-то окого 1 м.
Перемножая все константы, получаем:
T (кг · м) = 6207 x φ (рад) / L (м)
Прямая зависимость угла от вращающего момента и обратная для момента от длины оси руля. Например, чтобы свернуть мою ось на 1° или π/180 рад, потребуется усилие 108 кг · м.
Если бы я использовал цельную ось, а не трубу, то изменился бы только полярный момент инерции
J = (π/32) x do4 = 129 x 10-8 м4.
Таким образом, чтобы свернуть цельную ось такого же внешнего диаметра, что и труба, на тот же угол потребуется в 1,6 раза большее усилие.
Усиление скега внутри корпуса
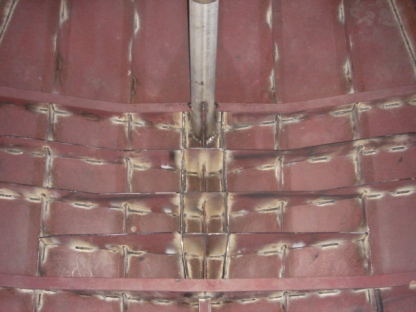
Как я уже говорил, между 9 и 10 шпангоутами в конструкции яхты отсутствуют поперечные детали набора. Это как раз там, где скег крепится к дну. То есть обычно скег просто отрывает кусок днища, когда отваливается. Помимо усиления самого скега с помощью вертикальных "шпангоутов" и "воротничка" в виде уголка из полоски 5 на 80, усиление днища просто необходимо.
Таким образом, внутри над "воротничком" я наварил продолжение скега и пустил три поперечных ребра жесткости, располагая их над вертикальными "шпангоутами" скега. Ребра жесткости я изготовил из 5 мм стали, маштабируя 9 и 10 шпангоуты в автокаде. Как видно на фото, все три пересекаются с продольными элементами и имеют отверстия для слива воды с внешней стороны замков. Первое ребро расходится на пару футов в обе стороны, два других - на три и доходят почти до скулы.
Выглядит все довольно прочно. Скег скорее сам сломается, но дно не оторвет.
Если скег хорошенько пнуть по нижней части, то он будет дрожать как струна в течении нескольких секунд. Таким образом, ось руля в районе нижнего подшипника должна изгибаться на пару см в обе стороны, но без постоянной деформации.