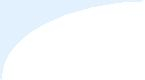
Choosing the material
Hull material: steel, wood, fiberglass or aluminum
Among these four, I have chosen steel, primarilly for its strength or low maintenance compared to wood, for example.
Aluminum scared me with its problematic welding. Any references that I found for aluminum, all linked to welding experience. They suggested under no circumstances to build a boat from aluminum without solid welding background, which I din't have. Also, the fact that aluminum becomes weaker after being heated, further distracted my attention from this material as oppose to steel welds that can potentially be made stronger than the welded material. I recognized the advantages of using aluminum such as its weight, which ironically couldn't overweight the advantages of steel still.
Fiberglass was rejected due to a difficulty of a mold construction, which didn't make sense for a single boat project.
Shipbuilding steel
Pre-cut kits that Bruce Roberts supplies are made from Lloyd's Grade A shipbuilding steel, which has the following properties:
C | Mn | Si | S | P |
---|---|---|---|---|
<= 0.21 % | >= 2.5 x Cmin % | <= 0.5 % | <= 0.035 % | <= 0.035 % |
Yield Point | Tensile Strength | Elongation at rupture |
---|---|---|
>= 235 N/mm2 | 440 - 490 N/mm2 | >= 22 % |
Although mechanical properties of Lloyd's grade A steel are similar to other low carbon steel grades, its chemical composition is quite remarkable as it is almost free of other elements commonly found in most grades of structural steel such as Al, N and Cu. Minimum amount of impurities is a key factor in avoiding galvanic corrosion.
Besides the excelent shipbuilding material, all parts in Bruce Roberts' kit are shotblasted and primed with weldable Sigmaweld MC primer.
Stainless steel
Many components of a steel boat are made of stainless steel; for example, rudder stock, propeller shaft, water tanks, chainplates, etc.
Stainless steel is corrosion resistant due to its chromium content. Chromium, when combined with oxygen, forms relatively inert (passivated) skin. Addition of nickel further enhances corrosion resistance. Stainless steel that has large amount of nickel is called austenitic. It can be identified by its non-magnetic property.
The other two broad categories of stainless steel without nickel - ferritic and martensitic, are magnetic. They have no use in marine environment.
To avoid corrosion, it is very important to select marine grade stainless steel. Generally 300 series SS is acceptable. The list below is sorted from less to more preferred (or from less to more corrosion resistant):
- 304 (>=18% of Cr and 8% of Ni)
- 316 (304 with added 2% of Mo for pitting resistance)
- 317 (304 with added 3% of Mo for increased pitting resistance)
- Nitronic 50 or Aquamet (22% of Cr and 12.5% of Ni)
- Al-6N, 254-S, 904L (6% of Mo and 20% of Ni)
When welding of stainless steel is required, only low carbon grade (304L, 316L, 317L, 904L) should be used because heat produced by welding causes carbon to combine with chromium effectively removing chromium from its passivating protective film forming role.
Galvanic series
It is very important to know the difference between electro-chemical potential of dissimilar metals that are in contact with each other. The more the difference, the higher the current it produces if submerged in seawater and the faster the corrosion will be of a metal with the lower potential (anode).
For example, the stainless steel area with the broken passivated film, which is often caused by oxigen starvation in stagnant seawater, will have its potential significantly lower than the rest of the material. The large cathodic area will cause rapid destruction of small anodic spots.
Common methods of preventing the galvanic corrosion are to electrically isolate dissimilar metals or at least to have anodes much larger than cathodes because small cathode would destroy large anode much slower. Therefore, it is acceptable to have stainless fittings such as chainplates and rudder stock welded on mild steel boats.
As for stainless steel, it is crucial to supply it with oxygen and caulk spaces where water can be trapped with waterproof compounds (see Links). Alternatively, SS fasterners in such places may be replaced with bronze ones. To avoid corrosion in propeller and rudder shafts sail a boat at least once a week to refresh the oxigen content in those places.
Metal or Alloy | Potential Relative to Silver/Silver Chloride Half Cell, V |
---|---|
Zinc | -0.98 to -1.03 |
Aluminum Alloys | -0.76 to -1.00 |
Mild Steel | -0.60 to -0.71 |
SS 410 without oxide layer (active in still water) | -0.46 to -0.58 |
SS 304 without oxide layer (active in still water) | -0.46 to -0.58 |
SS 316, 317 without oxide layer (active in still water) | -0.43 to -0.54 |
Aluminum Bronze (92% Cu, 8% Al) | -0.31 to -0.42 |
Naval Brass (60% Cu, 39% Zn) | -0.30 to -0.40 |
Yellow Brass (65% Cu, 35% Zn) | -0.30 to -0.40 |
Red Brass (85% Cu, 15% Zn) | -0.30 to -0.40 |
Tin | -0.31 to -0.33 |
Copper | -0.30 to -0.57 |
50-50 Lead/Tin solder | -0.28 to -0.37 |
Admiralty Brass (71% Cu, 28% Zn, 1% Sn) | -0.28 to -0.36 |
Aluminum Brass (76% Cu, 22% Zn, 2% Al) | -0.28 to -0.36 |
Manganeze Bronze (58.5% Cu, 39% Zn, 1% Sn, 1% Fe, 0.3% Mn) | -0.27 to -0.34 |
Silicon Bronze (96% Cu, 1.5% Zn, 2% Si, 0.8% Fe, 0.75% Mn, 1.6% Sn) | -0.26 to -0.29 |
Bronze Composition G (88% Cu, 2% Zn, 10% Sn) | -0.24 to -0.31 |
Bronze Composition M (88% Cu, 3% Zn, 6.5% Sn, 1.5% Pb) | -0.24 to -0.31 |
SS 410 (passive) | -0.26 to -0.35 |
Lead | -0.19 to -0.25 |
SS 304 (passive) | -0.05 to -0.10 |
SS 316, 317 (passive) | 0.00 to -0.10 |