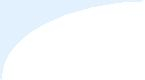
Placing the order
Getting the kit cut locally
As I said earlier, I had purchased the cutting files on a CD hoping to find a local metal shop to cut the kit. One would never think that it would be problematic especially in Edmonton with its booming oil industry and lots of metal shops. I was recommended Russel Metals as a steel supplier. They also had CNC cutting facilities.
By design, the kit was supposed to be cut from 4, 5 and 6 mm shipbuilding steel carried Lloyd's certificate. Therefore, all 350 parts in AutoCAD files had already been nested on metrical size plates, which were not common in North America.
First, Russel didn't carry shipbuilding steel in Edmonton, which I understood. Ordering 8 plates of it from a manufacture in Toronto was not feasible for them. So I would have built from similar steel (CSA G40.21 44W) but without Lloyd's certificate.
Second, the kit had to be converted to imperial dimensions. Basically, 4mm plates ought to be replaced with 3/16" plates and 5 and 6 mm plates with 1/4". Also, all parts had to be renested on the plate sizes that Russel supplied. In order to do that, the parts had to be separated into individual AutoCAD files.
It was time to learn AutoCAD. It didn't take me long to learn a number of most common AutoCAD functions but I spent a couple of weeks segregating each piece into a its own file. At that time Russel had said nothing about overall dimensions that they suddenly required later to give me a quote. They also specified other drawing requirements that I had to fulfil.
Finally, I got a quote for steel plates, cutting and bending and it looked good, at least better than buying a kit from Bruce Roberts. However, one critical piece was missing - priming was not on a quote. Priming had been important for me because I wanted to avoid expensive sandblasting during the pre-painting stages of my project.
I called Russel in Edmonton and they said that they neither prime nor supply pre-primed steel. I thought that this was not a big deal and that I could sandblast and prime parts later after they had been cut. Prior to commiting the project to Russel, I decided to check on blasting and priming in a painting shop. It took them a few days to calculate the price for 350 pieces of steel. Their quote had almost killed me. It was over $10,000.
They explained it by lots of manual labour required to blast and prime individual pieces. They admitted that it would have been much cheaper to blast and prime whole plates before cutting.
Ok, I thought, I would get plates from Russel, then truck them to a paint shop and then bring them back to Russel for cutting. I called Russel to make an arrangement but they said that they couldn't cut primed steel due to healthy concerns with paint vapors. Even after I provided them with the Sigmaweld MC health certificate, they refused to do the job.
I decided to check other Russel Metals' offices. When I called A. J. Forsyth in Vancouver I was surprised that they could do everything. They could subcontract a painting shop to wheelabrate and prime plates, they were going to cut and bend them later and deliver to me by train in a week. Perfect! I sent them cutting files. That was the end of my joy. It took them two months to give me a quote instead of promised one week. And in the quote, they said that they were sorry about radius plates, they couldn't bend them because there had not been enough information on the submitted drawings. I provided them the requested info next day and I hadn't heard from them since then. Every time I called them, I heard familiar "next week". I gave up after trying it for another month.
My frustration grew as I hadn't gotten any responses from Russel Metals offices in other provinces at all.
I had almost given up. I tried shops that use laser and water jet cutting but their tables were too small to cut my kit. I even thought to sandblast and prime myself. An estimated cost of renting a compressor or paying for the sandblasting made the total price very close to the price of Bruce's kit.
All my efforts to get the kit cut locally were useless.
What a relief it was when one day I had finally ordered the kit, cut from the designed metric size plates, made from the shipbuilding steel carried Lloyd's certificate, pre-primed with weldable zinc-rich Sigmaweld MC primer, with radius plates formed in both dimensions... from Bruce Roberts.